一 、加工产品
该案例加工产品为汽车差速器的内星轮,加工部位为内星轮内花键,材料为:16MnCr5,具体见下图:
二、 工件加工工艺要求
此工件在拉削内花键前的上一道工序为车削内孔和两端面,并保证拉前孔的尺寸精度和形位误差的要求,生产节拍要求为5秒/件,整个生产线为自动上下料的智能生产线。上料间隔时间大于20分钟。
三 、拉床及自动上下料连线的方案确定
由于客户产品为饼形套类零件,客户要求的产能节拍很高,所以我们选择了拉床类型为立式数控下拉四工位拉床,经拉力计算,实际拉削所需拉力位15吨,考虑到客户后期加工产品的扩展以及设备能力的储备,推荐使用了数控下拉式内拉床,四工位25吨,型号为:BS25SS4VHB,自动上料采用回转料仓,桁架机械手搬运,工件自动推料至下输送线,由下输送线送至清洗机。生产连线见下图:
四、 拉床的结构和配置
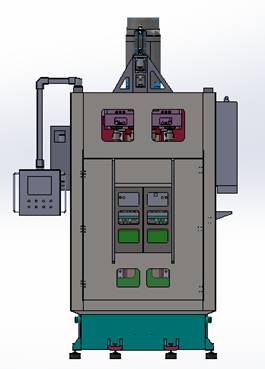
数控下拉式四工位内拉床外形
设备名称:数控下拉式内拉床;设备型号:BS25SS4VH;机床安装方式:地面式安装,上下料高度1350mm,按钮站高度1400-1500mm本机床为4工位机床,满足一次拉削4个零件。采用半封闭大罩,安全环保。上卡位与主滑板为同一平面上,刚性高,无偏摆,确保抓刀精准。该机床属于全护送立式内拉床,在拉削过程中采用工作台固定、拉刀运动的方式实现护送(即拉削工件时,上夹头松开护着后刀柄、下夹头夹紧拉刀前柄不松开,直至工件拉削快完成时,上夹头才脱开后刀柄)。机床结构选用全新的重载直线导轨副实现主滑板上下运动.拉刀接刀或送刀由上卡位刀座采用伺服驱动,主、辅线轨共面,保证机床的拉削精度。机床的操作系统采用按钮站操作,配合触摸屏能实现每个动作的单独调整机床位移的变化。机床拉削速度或返回速度采用伺服电机进行控制,可在触摸屏中按照指定工件进行切换设定,通过人机界面能直观地观察到在拉削过程中工作拉力变化值和各种状态,对于各种故障能自动显示出故障的所在位置且给予报警。
床身、床台、立柱均采用高性能钢板焊接而成,刚性高,吸震性好,并经过多次人工时效处理,以确保机床的精度的稳定性。机床各部分密封良好,保证无漏油现象。立柱与工作台稳定的结合在床身上,工作台上面装有定位基准金,其表面安装在工作台孔内。底座作为机床的支承件,具有很高的刚性,在它的内部装有冷却液,侧面装有冷却装置,自动排屑器装于立柱下方。
主溜板导轨和辅助溜板采用直线导轨,导轨刚性好、加工精度高,颠覆力矩小。
辅助溜板通过伺服电机实现卡刀体的送刀及提刀动作。
本机床无需挖地坑,直接采用地面安装式,在公称拉力和溜板行程的范围内,由伺服电机驱动主溜板运动。
机床的整个循环过程为:绗架机械手自动上料→送刀→下夹头夹刀→主滑板向下运动、→上夹头松开完成拉削(中途辅滑板带动上夹头让刀)→推料板推料下料→主滑板向上返回(中途辅滑板带动上夹头接刀)→主夹刀松开→上夹头向上提刀,完成一次循环。
电气系统
电气系统符合GB/T5226.1-2008国家标准。
电气柜密封性好,内有照明灯和热交换器,并保证电箱温度升在400C以下,电箱门设有开门断电保护。
触摸屏采用欧姆龙品牌产品,可编程序控制器采用西门子,低压电器控制元件采用国产优质产品。
主要技术参数
序号 |
规格名称 |
单位 |
数值 |
1 |
额定拉力 |
KN |
250 |
2 |
最大行程 |
mm |
800 |
3 |
适用拉刀长度 |
mm |
750-880 |
4 |
机床工位数 |
|
4 |
5 |
主溜板 |
工作行程速度(无级变速) |
m/min |
2-8 |
返回行程速度(无级变速) |
m/min |
2-10 |
工作台面尺寸 |
mm |
750x350 |
地面至工作台面距离 |
mm |
1430 |
6 |
辅助溜板 |
最大工作行程 |
mm |
500 |
拉刀送进 |
m/min |
3-6 |
拉刀返回 |
m/min |
3-8 |
7 |
刀柄端面到工作台面最小距离 |
mm |
200 |
8 |
主电机功率 |
Kw |
28-30 |
9 |
辅助伺服电机 |
Kw |
2 |
10 |
冷却泵功率 |
KW |
2.2 |
11 |
机床总功率 |
KW |
约40 |
12 |
外形尺寸(长、宽、高) |
mm |
2500×1900×4600 |
13 |
机床重量 |
kg |
约8000 |
五、 拉床自动生产线的实际使用效果
该自动生产线在客户工厂使用了近一年多,所生产的零件均符合客户的各项技术要求,生产节拍为19秒/4件,满足客户5秒/件的节拍要求。