一 、加工产品
该案例加工产品为电动工具的轴套,加工部位为轴套异形孔,材料为:20CrMo,具体见下图:
二、 零件加工工艺要求与加工难点
零件拉前孔很小,而拉削深度又很深,如果通过一次拉削成型刀具强度难以做到,且刀具长度较长。零件硬度HB190-220,拉削性能合理。
拉削工艺要求:除图纸上的尺寸精度要求外,其异形孔表面粗糙度不得小与3.2,且无震纹,生产节拍为16秒/件。
三、 拉床方案确定
由于客户产品异形孔的拉削深度较深,一次拉削成型刀具强度难以保证,因此我们采用二次拉削成型的拉削方案。由于上拉式拉床对二次拉削定位有独特的优点,故选用上拉式内拉床的方案,经拉力计算和客户节拍的要求以及客户后期加工产品的扩展以及设备能力的储备,我们推荐使用了立式数控上拉双工位10吨拉床,型号为:BS10SS2VHT,人工上料自动推料下料。
四、 拉床的结构和配置
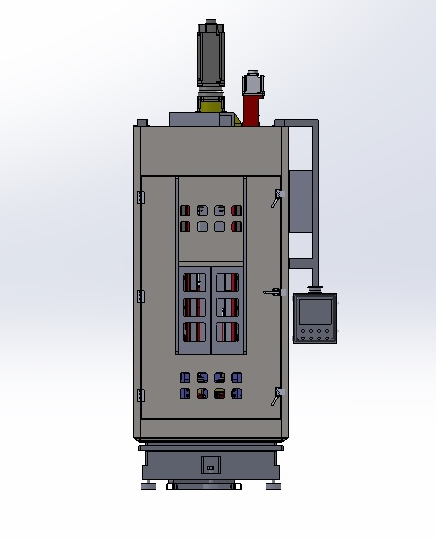
拉床外形图
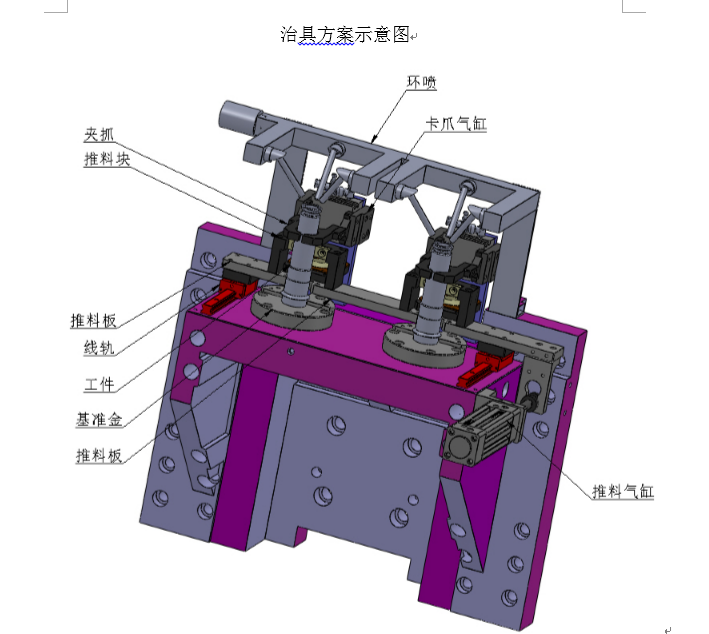
治具图
机床属于全护送立式内拉床,在拉削过程中采用拉刀固定、工件运动的方式实现全护送,机床结构选用重载直线滚珠导轨副实现工作台上下运动.拉刀接刀或送刀由上卡位刀座采用共轨伺服电机实现,保证机床的拉削精度。
机床的操作系统采用按钮站控制,能实现每个动作的单独调整、机床位移的变化。机床拉削速度或返回速度采用伺服电机来控制,可在电气柜中电位器旋钮任意设定。机床采用触摸屏控制,通过人机界面能直观地观察到在拉削过程中工作拉力变化值和各种状态。对于各种故障能自动显示出故障的所在位置且给予报警。拉削速度均可在操作屏上通过触摸键任意设定。
床身采用孕育铸铁经树脂砂铸造而成,刚性高,吸震性好,并经过多次人工时效处理,以保证机床的精度的稳定性。床台、立柱、上下卡位本体等均采用高强度钢板焊接而成,并经多道人工时效,以保证其精度持久性。机床各部分密封良好,保证无漏油现象。工作台固定在主滑板上,工作台上面装有定位基准筋,其表面安装在工作台孔内。底座作为机床的支承件,具有很高的刚性,在它的内部装有冷却液,侧面装有冷却装置,自动排屑器装于立柱下方。
主溜板导轨和辅助溜板采用共轨直线导轨,导轨刚性好、颠覆力矩小
辅助溜板通过伺服电机实现卡刀体的送刀及提刀动作。
主辅夹刀体均采用钢件,卡爪均采用合金钢,淬火硬度高,自定心夹紧。主夹刀体和辅夹刀体均为气缸夹紧式,经过气缸带动一套机构夹持拉刀柄部,随辅溜板一起运动。
本机床采用伺服电传动,工作平稳,能无级调速;机床的拉削方式为工件固定在工作台上,主滑板由伺服电机带动滚珠丝杆上、下移动实现拉削,机床有全程护送刀装置;有自动循环、半自动循环及调整三种操作方式,能适应不同拉削形式的需要。
机床的整个循环过程为:人工上料(二次精拉时须采用定位机构)→送刀→下夹头夹刀→主滑板向上运动、→上夹头松开完成拉削(中途辅滑板带动上夹头让刀)→人工下料→主滑板向下返回(中途辅滑板带动上夹头接刀)→主夹刀松开→上夹头向下提刀,完成一次循环。
该机床设有二此精拉定位机构,此机构为我公司的专利产品。
机床电气系统符合GB/T5226.1-2008国家标准。电气柜密封性好,内有照明灯和冷却风扇,并保证电箱温度在400C以下,电箱门设有开门断电保护。
触摸屏采用步科(或欧姆龙)品牌、可编程序控制器采用西门子产品,低压电器控制元件采用国产优质产品
主要技术参数
序号 |
规格名称 |
单位 |
数值 |
1 |
额定拉力 |
KN |
100 |
2 |
最大行程 |
mm |
1400 |
3 |
适用拉刀长度(工件高度≤250mm) |
mm |
750-1450 |
4 |
机床工位数 |
|
2 |
5 |
主溜板 |
工作行程速度(无级变速) |
m/min |
2-8 |
返回行程速度(无级变速) |
m/min |
2-12 |
工作台面尺寸 |
mm |
190×410 |
地面至工作台面距离 |
mm |
1150 |
工作台孔径 |
mm |
Φ70 |
6 |
辅助溜板 |
最大工作行程 |
mm |
650 |
拉刀送进 |
m/min |
3-8 |
拉刀返回 |
m/min |
3-10 |
7 |
刀柄端面到工作台面距离 |
mm |
210 |
8 |
主电机功率 |
KW |
11 |
9 |
辅电机功率 |
KW |
2 |
10 |
冷却泵功率 |
KW |
2.2 |
11 |
机床总功率 |
KW |
约15 |
12 |
外形尺寸(长、宽、高) |
mm |
2050×3000×3700 |
13 |
机床重量 |
kg |
约4000 |
五、 拉床的实际使用效果
该数控上拉式内拉床所生产的零件均符合客户的各项技术要求,生产节拍为32秒/2件,满足客户16秒/件的节拍要求。